28 Mar
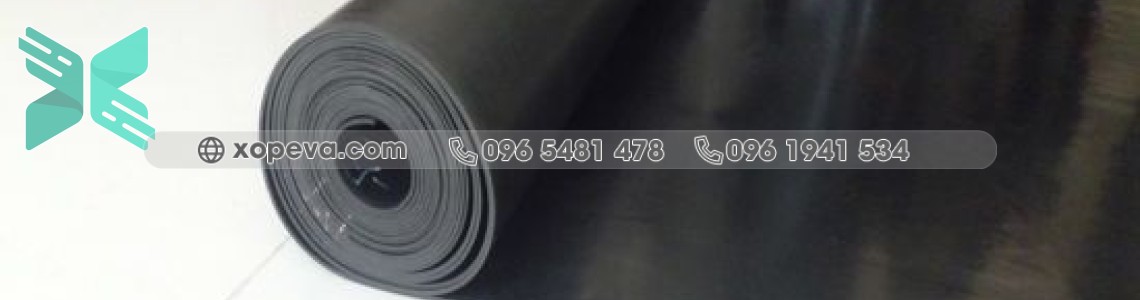
0 Comment(s)
1744 View(s)
EPDM rubber and NBR rubber are both widely used in various industries for their unique properties. Here is a comparison between the two:
- Chemical resistance: EPDM rubber has excellent resistance to ozone, weathering, and UV rays, making it an ideal choice for outdoor applications. It also has good resistance to acids, alkalines, and oxygenated solvents. On the other hand, NBR rubber has excellent oil and fuel resistance, but is not suitable for applications with strong acids or alkalis.
- Temperature range: EPDM rubber can withstand temperatures ranging from -50°C to +150°C, while NBR rubber has a higher maximum temperature of up to +120°C but lower minimum temperature of -40°C.
- Compression set: EPDM rubber has a low compression set, meaning it can withstand deformation and return to its original shape, making it a good choice for sealing applications. NBR rubber has a higher compression set, meaning it may not recover its shape as well after compression.
- Tensile strength: NBR rubber has a higher tensile strength than EPDM rubber, making it more suitable for applications that require high mechanical strength.
In summary, EPDM rubber is better suited for outdoor applications and has good resistance to weathering and UV rays, while NBR rubber is better suited for applications that require oil and fuel resistance and higher mechanical strength. The choice between the two will ultimately depend on the specific requirements of the application
Leave a Comment