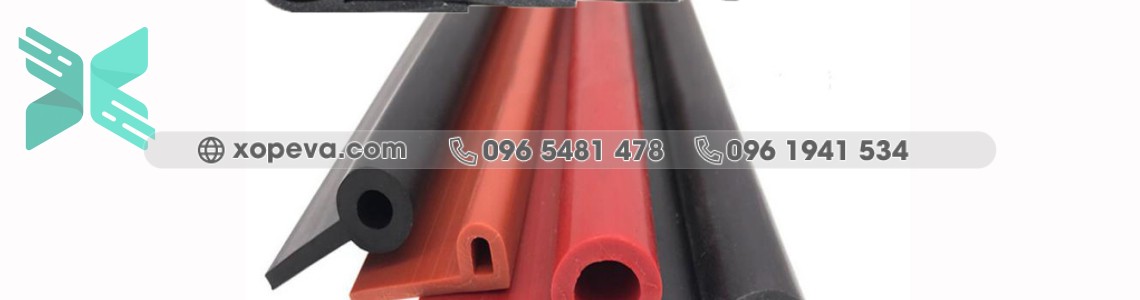
P-shaped rubber seals also known as garlic-shaped rubber seals, are a type of rubber seal that has a shape resembling the letter "P" when viewed from a cross-section. P-shaped rubber seals are commonly used to create a tight and secure connection in various applications within the hydroelectric, irrigation, and other industrial sectors.
P20, P30, P40, and P50 seals are typically made from synthetic rubber or silicone rubber, depending on the specific requirements of the application. They possess flexibility and elasticity, which effectively create an airtight or liquid-tight seal between two surfaces.
What is a rubber seal?
A rubber seal is an engineering component used to provide sealing or waterproofing in joints or connections between surfaces. It is made from synthetic rubber or natural rubber, with the flexibility and elasticity to create an airtight, liquid-tight seal or prevent the infiltration of dust, water, oil, and other fluids.
Rubber seals are commonly shaped as rings, gaskets, U-shapes, O-shapes, or other suitable forms based on the specific application requirements. They can withstand pressure, temperature, and other environmental factors during operation.
Characteristics of commonly used rubber types
Different rubber types have their own characteristics and applications. The selection of the appropriate rubber type depends on specific application requirements, including operating conditions, chemicals, durability and lifespan, required pressure, and elasticity. Some common applications of different rubber types are listed below:
• Natural rubber: Used in toy manufacturing, medical products, bicycle tire production, cargo straps, and various seals.
• Nitrile rubber: Used for manufacturing fuel hoses, oil spray nozzles, automotive parts, protective membranes, and various seals.
• EPDM rubber: Often used in waterproofing products, water hoses, conveyor belts, heat-resistant seals, water pipes, and vibration dampers.
• Silicone rubber: Used in the production of medical products, automotive components, vibration dampers, heat-resistant seals, and other heat-resistant products.
• Fluoroelastomer rubber: Typically used in the production of chemical-resistant conveyor belts, filters, automotive parts, chemical transfer hoses, valves, and chemical-resistant seals.
Choosing the appropriate rubber type is crucial to ensure the durability and effectiveness of the final product. Therefore, consumers should thoroughly research different rubber types and specific product requirements before deciding which rubber type to use
Function of P-shaped rubber gasket
A P-shaped rubber gasket serves the function of creating a seal and securely holding the joint between two surfaces. Here are some key functions of a P-shaped rubber gasket:
1. Fluid sealing: The P-shaped rubber gasket is designed to prevent leakage or intrusion of liquids such as water, oil, gas, or chemicals in industrial applications. It is placed in joints or gaps between surfaces to form a tight barrier.
2. Waterproofing: P-shaped rubber gaskets have the ability to resist water and prevent the ingress of water, dust, dirt, and other liquids into joints. This is particularly important in applications where protection against the external environment is required.
3. Pressure and temperature resistance: P-shaped rubber gaskets are manufactured from high-quality rubber materials that can withstand different pressures and temperatures during operation. It has flexibility and elasticity, allowing it to adapt to the changes in the joint without deforming or getting damaged.
4. Vibration and noise reduction: P-shaped rubber gaskets also have the ability to dampen vibration and noise in applications where there is oscillation or shock. When placed in joints, it helps reduce the transmission of vibrational movement and noise from one surface to another, ensuring smooth operation and minimizing unwanted noise.
In summary, P-shaped rubber gaskets are crucial components in industrial applications, aiding in sealing, waterproofing, pressure and temperature resistance, as well as reducing vibration and noise in the joint between surfaces.
Applications of P-shaped rubber gaskets
P-shaped rubber gaskets have numerous applications in various industries and fluid handling. Here are some examples of the applications of P-shaped rubber gaskets:
1. Automotive industry: P-shaped rubber gaskets are used in the engine system, cooling system, fuel system, and exhaust system of automobiles. It provides a tight seal, prevents liquid leakage, and withstands high temperatures and pressures.
2. Chemical industry: P-shaped rubber gaskets are used in chemical equipment and piping to seal and prevent the leakage of chemical liquids. They must withstand the impact of chemicals and high temperatures.
3. Oil and gas industry: P-shaped rubber gaskets are used in oil and gas pipelines to seal and prevent oil and gas leakage. They must withstand high pressure, temperature, and the harsh environment of the oil and gas industry.
4. Electronics industry: P-shaped rubber gaskets are used in electronic devices to seal and protect against dust, water, and other environmental agents. They also have the ability to withstand voltage and temperature.
5. Food and medical industry: P-shaped rubber gaskets are safe for use in applications related to food and medical industries. They are used in medical devices, food processing machinery, and pipeline systems related to this industry.
6. Other industrial applications: P-shaped rubber gaskets can also be used in other industrial sectors such as machinery manufacturing, air conditioning, water treatment systems, the paper industry, and other industrial applications.
The applications of P-shaped rubber gaskets depend on the specific requirements of each industry and specific application.
Quality standards for P-shaped rubber gaskets
Quality standards for P-shaped rubber gaskets may vary depending on the industry and specific application. However, here are some common quality standards applied to P-shaped rubber gaskets:
1. Dimensional standards: P-shaped rubber gaskets must comply with accurate dimensional standards to ensure proper fit and precise sealing for the relevant joints or surfaces.
2. Hardness standards: The hardness of P-shaped rubber gaskets needs to be controlled to ensure appropriate flexibility and elasticity. This requires testing and evaluation using standard methods such as ASTM D2240 to measure the hardness of the rubber gasket.
3. Standards for high temperature resistance and rubber quality: The P-shaped rubber gasket must have the ability to withstand high temperatures and resist high-quality rubber. This includes testing for thermal stability, oil resistance, chemical resistance, and weather resistance, to ensure that the rubber gasket can operate stably in harsh environments.
4. Standards for waterproofing and sealing ability: The P-shaped rubber gasket must be tested to ensure good sealing and waterproofing ability under specific pressure and fluid conditions. This is often tested using standard methods such as ASTM F37 or ASTM F104, to measure the leakage rate of the rubber gasket.
5. Standards for safety and compliance: The P-shaped rubber gasket must comply with safety standards and regulations related to the specific industry and application. For example, in the healthcare industry, rubber gaskets must comply with standards such as FDA (US Food and Drug Administration) to ensure patient safety and health.
6. Standards for lifespan and durability: The P-shaped rubber gasket must have appropriate lifespan and durability to meet long-term use requirements. This includes testing and evaluating the ability to resist wear, impact, and age in different conditions.
7. Standards for production quality: The P-shaped rubber gasket must comply with general manufacturing process and quality standards. This ensures that the manufacturing process is carried out accurately, reliably, and ensures the final quality of the rubber gasket.
Quality standards for P-shaped rubber gaskets may vary across industries and specific applications. For each application, reliable testing and evaluation processes must be carried out to ensure that rubber gaskets meet specific requirements and operate safely and efficiently
How to select and use P-shaped rubber seals
When selecting and using P-shaped rubber gaskets, you can follow the following steps:
1. Determine application requirements: Firstly, clearly identify the specific requirements of the P-shaped rubber gasket application, including temperature, pressure, fluid or gas, chemical environment, impact resistance, and desired lifespan.
2. Identify suitable rubber material: Based on the application requirements, determine the appropriate type of rubber for the P-shaped gasket. Common rubber types such as natural rubber, nitrile rubber, EPDM rubber, silicone rubber, or fluoroelastomer rubber have different properties and are suitable for different applications.
3. Choose size and design: Determine the appropriate size and design for the P-shaped rubber gasket, including diameter, thickness, shape, and structure. Ensure that the gasket has dimensions and design suitable for the mating surfaces and sealing requirements.
4. Consider quality standards and regulatory compliance: Check if the P-shaped rubber gasket meets the necessary quality standards and regulatory compliance for the specific industry and application. Ensure that the rubber gasket is manufactured and certified according to the corresponding safety and quality standards.
5. Installation and maintenance: Install the P-shaped rubber gasket according to the manufacturer's instructions and procedures. Ensure that the gasket is properly fitted, without deformations or cracks. Perform regular maintenance to inspect and replace the gasket when necessary to maintain its sealing ability and performance.
6. Performance testing: Monitor the performance of the P-shaped rubber gasket during use. Test its sealing condition, temperature resistance, chemical resistance, and lifespan. Conduct regular inspections to ensure that the gasket still meets the requirements and shows no signs of damage.
7. Consultation from manufacturer or experts: If needed, consult with the manufacturer of the P-shaped rubber gasket or experts in the field for the best support in terms of selection, usage, and maintenance of the rubber gasket.
8. Order from reliable suppliers: Ensure that you order the P-shaped rubber gasket from reputable and reliable suppliers, guaranteeing quality and compliance with necessary standards.
9. Read and follow the user instructions: Read and carefully follow the manufacturer's instructions for the proper use and storage of the rubber gasket to ensure correct usage and prolong its lifespan.
10. Monitor and evaluate performance: Monitor and evaluate the performance of the P-shaped rubber gasket after each usage stage and implement appropriate maintenance measures to maintain good performance.
Properly selecting and using P-shaped rubber gaskets is crucial to ensure sealing ability and system performance. By following the above steps and thoroughly understanding the application requirements, you can effectively and reliably choose and use P-shaped rubber gaskets
Leave a Comment