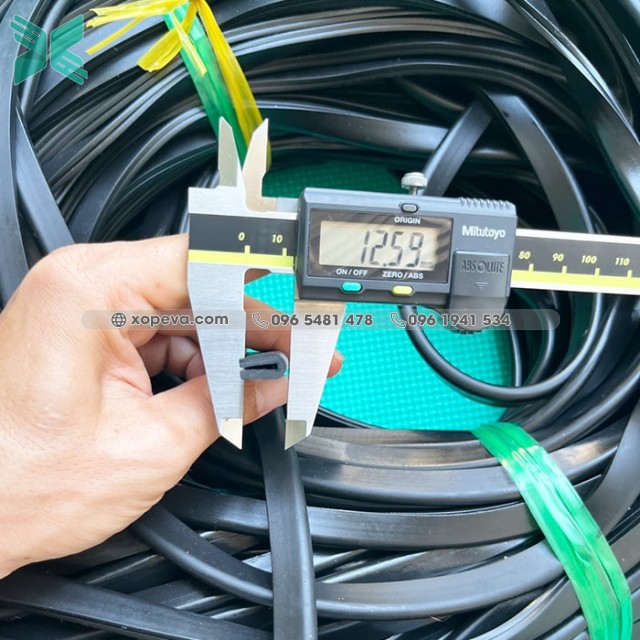
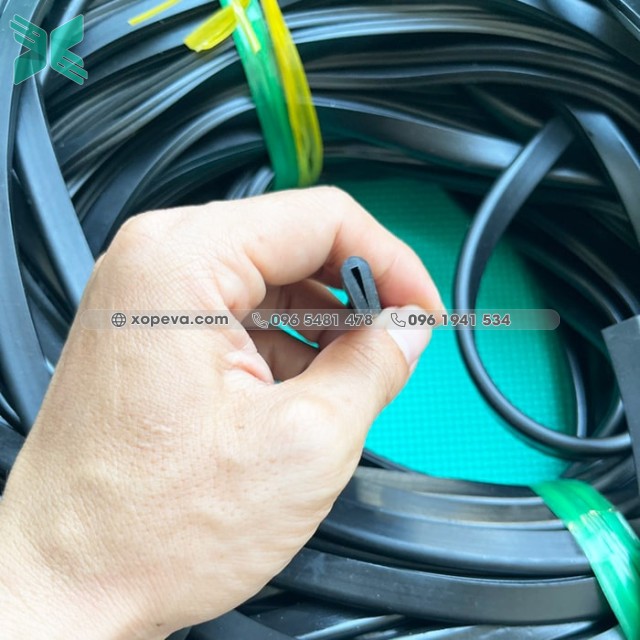
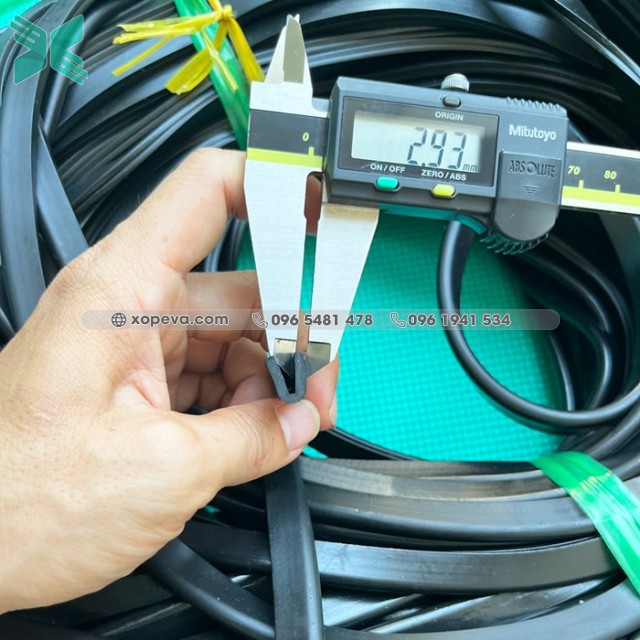
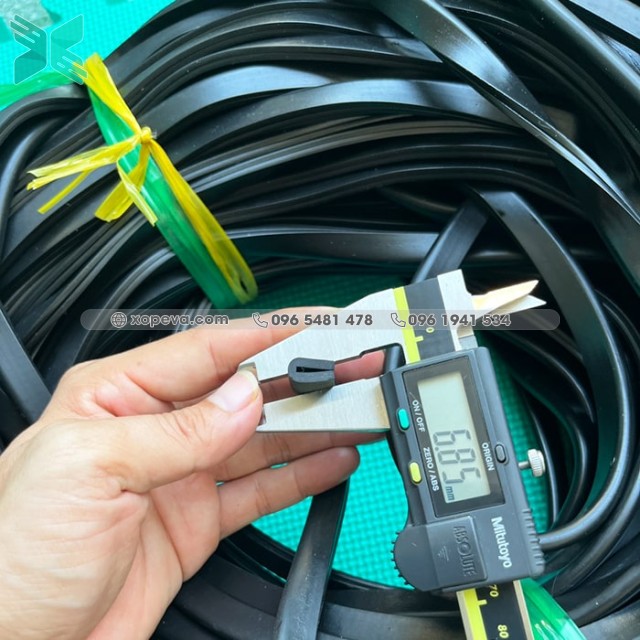




Material: | Standard Rubber |
Size: | 6mm x 12mm x 1.5mm |
Hardness (Shore A): | 50-75° |
Minimum length: | 50m |
Full coil length: | 100m |
Colour: | Black |
Estimated delivery: | 6 to 8 working days |
- Stock: In Stock
- Model: R7829_7
U-shaped Rubber Gaskets
U-shaped rubber gaskets are a type of rubber gasket that resembles the letter "U" when viewed from the top. They are used to create a tight seal or prevent leakage between two surfaces or components. U-shaped rubber gaskets are commonly made from synthetic rubber or silicone rubber because they can withstand high temperatures, oils, chemicals, and harsh working conditions. Additionally, U-shaped rubber has good flexibility and resilience, allowing it to easily expand and adjust to uneven or imperfect surfaces.
U-shaped rubber gaskets are commonly used in industrial and mechanical applications. For example, they can be used for sealing or waterproofing in water systems, oil conduits, machinery, pumps, and many other applications. U-shaped rubber gaskets have the ability to withstand pressure and resist abrasion, making them an essential component in various industries.
The design of U-shaped rubber gaskets is specifically aimed at creating a water-tight capability around the U-shaped space. This helps prevent leakage or water seepage through gaps or imperfect surfaces.
The applications of U-shaped rubber gaskets are diverse. They are frequently used in mechanical and electronic systems such as compressed air systems, piping systems, valves, pumps, machining equipment, industrial machinery, medical devices, and many other industries. U-shaped rubber gaskets are also commonly used in the automotive industry to provide sealing for components such as gearboxes, reservoirs, and cooling systems.
Using U-shaped rubber gaskets ensures the safety and performance of systems and equipment. They help prevent leaks, protect against direct contact with harmful fluids or gases, and reduce noise, vibration, and wear caused by collisions.
However, selecting and using U-shaped rubber gaskets correctly is crucial. The size, material, and design must be suitable for the specific application requirements to ensure optimal performance and long lifespan for the gasket. Additionally, proper installation and maintenance procedures are necessary to ensure the tightness and stable operation of the system.
U-shaped rubber gaskets can also be customized to meet specific application requirements. Technical specifications such as size, shape, and material can be adjusted to meet the specific needs of customers.
For certain specialized applications, U-shaped rubber gaskets can be reinforced with fabric layers or metal layers to enhance strength and pressure resistance. This is particularly useful in high-pressure or high-temperature applications where the gasket needs to withstand harsh environments.
The waterproofing and abrasion resistance features of U-shaped rubber gaskets also contribute to increased reliability and longevity of equipment and systems. This is particularly important in industries such as oil and gas, chemical, food, and water treatment, where leaks can have serious consequences for the environment and human safety.
Regular maintenance and replacement of U-shaped rubber gaskets are also essential to ensure maximum performance. Old, damaged, or deformed gaskets can lead to leakage and loss of system efficiency. Therefore, regular inspection and replacement of gaskets are necessary.
In conclusion, U-shaped rubber gaskets play a significant role in creating sealing and waterproofing in industrial and mechanical applications. They provide pressure resistance, heat resistance, and abrasion resistance, helping protect and enhance the performance of systems and equipment. However, selecting the right U-shaped rubber gasket and regular maintenance are important to ensure the tightness and stability of the system over the long term.
Specifications | |
Cao | |
Rộng | |
Thickness |