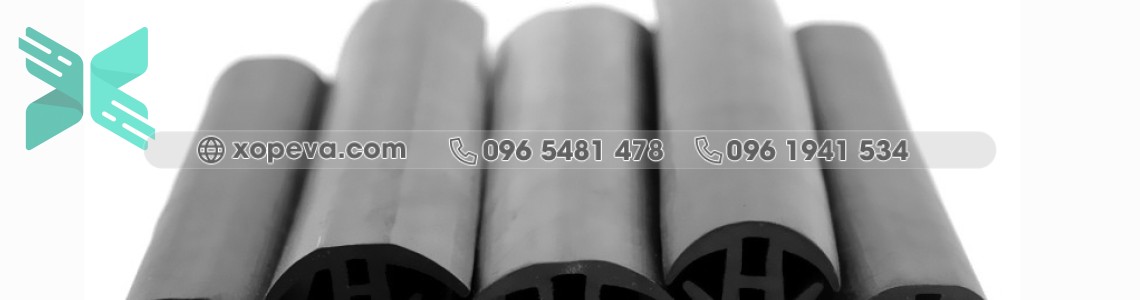
T-shaped rubber gaskets are a type of rubber gasket that has a shape resembling the letter "T" when viewed from above. They are used to create a tight seal between two different surfaces or components in industrial applications. T-shaped rubber gaskets are typically made from elastic rubber materials with good elasticity and insulation properties, such as synthetic rubber materials like NBR (Nitrile), EPDM, Silicone, FKM (Viton), etc.
T-shaped rubber gaskets are specially designed with a "T" groove running around the edge of the gasket, allowing it to be inserted into grooves or gaps to create a tight seal. This gasket has the ability to resist water, oil, chemicals, and has relatively good heat resistance, making it suitable for various industrial applications.
T-shaped rubber gaskets are commonly used in industries such as automotive, machinery, electronics, medical, chemical industry, water treatment, etc. They can be used to provide insulation, water resistance, vibration resistance, dust resistance, and ensure sealing in various applications.
Characteristics of T-shaped rubber gaskets
T-shaped rubber gaskets are a widely used product in industrial applications and have the following distinct characteristics:
1. Durability: T-shaped rubber gaskets have high durability and can withstand impacts from heat, pressure, collisions, and chemicals.
2. Elasticity: The rubber material used in T-shaped gaskets has high elasticity, allowing it to compress and stretch to create a tight seal between surfaces.
3. Waterproofing Capability: T-shaped rubber gaskets have waterproofing capabilities, creating a barrier against water, oil, liquids, and gases.
4. Heat Resistance: T-shaped rubber gaskets have good heat resistance and can withstand temperatures ranging from -50 to 150 degrees Celsius.
5. Insulation Properties: T-shaped rubber gaskets have insulation properties and can be used in medical and electronic applications.
6. Longevity: T-shaped rubber gaskets have a long lifespan, reducing maintenance and replacement costs.
7. Easy Installation: T-shaped rubber gaskets have a design that allows for easy installation and removal, saving time and costs.
Depending on the type of rubber material used to manufacture the T-shaped gaskets, these characteristics may vary slightly. However, in many cases, T-shaped rubber gaskets remain a good choice for industrial applications due to their outstanding properties
Types of T-shaped rubber gaskets
There are several popular types of T-shaped rubber gaskets used in industrial applications. Here are some examples:
1. Single T-shaped rubber gasket: This is a simple type of T-shaped gasket with a single T-shaped rubber strip running around the edge of the gasket. It is commonly used to create a tight seal between two surfaces.
2. Double T-shaped rubber gasket: The double T-shaped rubber gasket has two parallel T-shaped rubber strips. It provides better sealing capability and is suitable for applications with strict sealing requirements.
3. Electrically conductive/insulating T-shaped rubber gasket: This is a special version of the T-shaped rubber gasket reinforced with anti-static or conductive materials to prevent electrical interference in applications that require high electrical insulation.
4. Heat-resistant T-shaped rubber gasket: Heat-resistant T-shaped rubber gaskets are made from heat-resistant rubber materials such as Silicone, EPDM, or Viton. They have good heat resistance and are used in applications that require high temperature resistance.
5. Chemical-resistant T-shaped rubber gasket: Chemical-resistant T-shaped rubber gaskets are made from rubber materials that can withstand aggressive chemicals. Suitable materials include Viton, EPDM, or Nitrile, depending on the specific chemical resistance required.
6. Water-resistant T-shaped rubber gasket: Water-resistant T-shaped rubber gaskets are specially designed to create a watertight seal. They are commonly used in water treatment applications, water tanks, drainage systems, etc.
Note that there are many different types of T-shaped rubber gaskets, and their materials and designs may vary depending on the specific requirements and conditions of the application they are used in. Additionally, many manufacturers can customize the design and material of T-shaped rubber gaskets to meet specific customer requirements.
Applications of T-shaped rubber gaskets
Some specific examples of T-shaped rubber gasket applications in various industries include:
• In the oil and gas industry: T-shaped rubber gaskets are used for sealing in oil and gas pipelines, oil filters, valves, pumps, etc. Chemical-resistant and heat-resistant T-shaped rubber gaskets are commonly used in this industry.
• In the automotive industry: T-shaped rubber gaskets are used in various parts of automotive engines, including cooling systems, powertrain systems, brake systems, and exhaust systems. Heat-resistant and oil-resistant T-shaped rubber gaskets are commonly used in the automotive industry.
• In the electronics industry: Electrically conductive T-shaped rubber gaskets are used in electronic applications, including electronic devices in automobiles, computers, and mobile devices.
• In the food and beverage industry: T-shaped rubber gaskets are used in food and beverage piping systems to ensure tight sealing and prevent contamination from other liquids. Oil-resistant and non-toxic T-shaped rubber gaskets are commonly used in this industry.
• In the medical industry: T-shaped rubber gaskets are used in medical devices such as blood pressure monitors, infusion pumps, and other medical diagnostic equipment. Non-toxic and heat-resistant T-shaped rubber gaskets are commonly used in the medical industry.
These are some examples of the applications of T-shaped rubber gaskets in various industries. Depending on the requirements of each application and specific working environments, there may exist various types of T-shaped rubber gaskets
Technical Standards for T-shaped Gaskets
Common issues when using T-shaped rubber gaskets and their remedies
When using T-shaped rubber gaskets, several common issues may arise. Here are some common issues and their remedies:
1. Leakage: Leakage occurs when the gasket fails to provide a perfect seal between two surfaces. To address this issue, the following measures can be taken:
• Verify the correct dimensions and design of the gasket. • Ensure proper tension and compression of the gasket during installation. • Use gaskets made from materials suitable for the working conditions and fluids in the system.
2. Wear and damage: T-shaped rubber gaskets can wear out and become damaged due to pressure, temperature, and fluids. To address this issue, the following measures can be applied:
• Use gaskets with materials that are resistant to wear and can withstand the specific application. • Ensure proper lubrication between the gasket and mating surface in terms of quantity and quality. • Regularly inspect and replace gaskets to prevent unnecessary wear and damage.
3. Chemical compatibility: T-shaped rubber gaskets can be affected by chemicals, leading to degradation, swelling, or reduced durability. To address this issue, the following measures can be taken:
• Use gaskets made from materials that are compatible with the chemicals they will come into contact with. • Inspect and understand the chemical properties of the fluid or working environment before selecting gaskets. • Ensure proper technical replacement of gaskets according to the maintenance schedule.
4. Elasticity and flexibility: Over time, T-shaped rubber gaskets may lose their elasticity and flexibility. This can result in expansion, leakage, or compromised sealing. To address this issue, the following measures can be applied:
• Regularly inspect and replace gaskets to maintain optimal elasticity and flexibility. • Use rubber gaskets that can withstand deformation and aging over time. • Select gaskets with heat resistance and ozone resistance to ensure longevity in the working environment.
5. Installation errors: Incorrect installation of T-shaped rubber gaskets can lead to issues such as leakage, inadequate sealing, or gasket damage. To address this issue, the following measures can be applied:
• Follow the manufacturer's recommended installation procedure. • Ensure proper tension and compression of the gasket during installation. • Inspect and confirm that the gasket installation has been carried out correctly and accurately.
6. Durability and lifespan: T-shaped rubber gaskets undergo wear and have limited lifespan based on application requirements and working conditions. To enhance durability and lifespan, the following measures can be applied:
• Select rubber gaskets with materials and designs suitable for the application requirements. • Perform regular maintenance and inspection of gaskets to detect and replace damaged gaskets promptly.
• Apply proper operation and storage procedures to ensure maximum lifespan for the gaskets.
However, it should be noted that each specific issue and remedy may vary depending on the application and working conditions. For complex or unresolvable issues, it is advisable to consult the rubber gasket manufacturer or technical experts for specific guidance and support. Rubber gasket manufacturers and technical experts have the knowledge and experience to provide optimal solutions for T-shaped rubber gasket-related issues
Common Issues When Using Rubber Gaskets
In addition, to avoid common issues when using T-shaped rubber gaskets, it is important to adhere to the following rules and guidelines:
1. Choose quality gaskets: Select rubber gaskets from reputable manufacturers and ensure product quality. Use certified rubber gaskets that meet the necessary quality standards for specific applications.
2. Ensure clean and flat surfaces: Before installing the gasket, ensure that the working surface is clean and flat. Any debris, dirt, or grease can damage the gasket or reduce its sealing capability.
3. Perform thorough pre- and post-installation checks: Conduct a thorough inspection of the gasket before installation to ensure there are no damages or manufacturing defects. After installation, perform a meticulous check to ensure proper sealing and operational performance of the gasket.
4. Follow installation instructions: Read and follow the installation instructions provided by the manufacturer. Installing the gasket according to the correct procedure will help ensure proper sealing and prevent any potential issues.
5. Regular maintenance: Perform regular maintenance and inspection of the gasket to detect early signs of wear, damage, or aging. Replace damaged or expired gaskets promptly to ensure system performance and safety.
6. Seek expert advice: If faced with complex issues or problems that cannot be resolved independently, seek advice from technical experts or rubber gasket manufacturers. These experts have in-depth knowledge of rubber gaskets and can provide customized solutions based on your specific requirements and conditions.
Finally, conducting regular checks and scheduled maintenance is crucial to ensure the performance and longevity of T-shaped rubber gaskets. Schedule regular inspections and maintenance to identify any damage and replace gaskets as necessary. This helps avoid potential issues and ensures the stable operation of the system.
When encountering issues with T-shaped rubber gaskets, the most important thing is not to overlook the problem. Learn and understand your application, working environment, and requirements in order to choose and use rubber gaskets correctly. If needed, seek advice and support from rubber gasket manufacturers or technical experts to ensure your success and safety in using T-shaped rubber gaskets
Leave a Comment