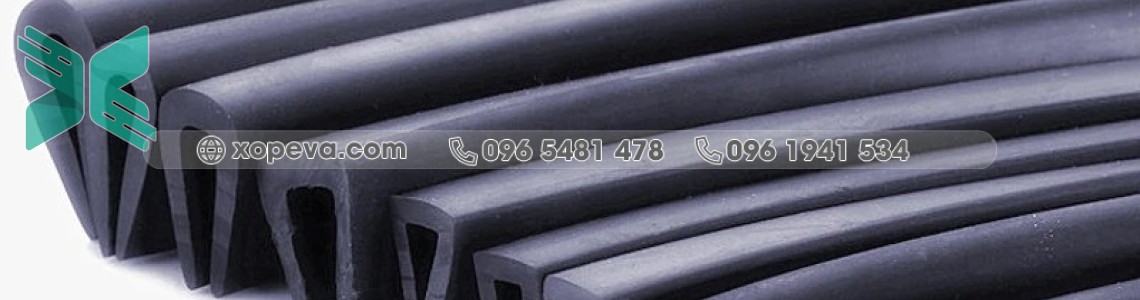
U-shaped rubber gasket, also known as U-shaped rubber seal, is a type of gasket used in various industrial applications. The U-shaped rubber gasket has a shape resembling the letter "U" when viewed from the outside.
U-shaped rubber gaskets are typically made from synthetic rubber or silicone rubber, depending on specific usage requirements. They have heat resistance, oil resistance, chemical resistance, and good elasticity.
U-shaped rubber gaskets are commonly used for sealing or insulation purposes in mechanical and industrial applications, such as in fluid conduits, machinery, electronic devices, automobiles, motorcycles, and many other applications.
Understanding Rubber Gaskets
Rubber gaskets are mechanical components used for sealing, insulating, or preventing leaks in industrial applications. They are made from synthetic rubber or natural rubber materials, which possess the ability to expand and contract to create a seal between surfaces or gaps in mechanical systems, equipment, tanks, fluid conduits, and various other applications.
Rubber gaskets are designed to withstand different pressures, temperatures, and environmental impacts. They are resistant to oils, chemicals, and certain extreme substances. Rubber gaskets are flexible and can compress and adapt to uneven surfaces, ensuring a perfect seal.
Common types of rubber gaskets include O-ring gaskets, U-shaped gaskets, D-shaped gaskets, flat gaskets, and various other types depending on specific application requirements.
Rubber gaskets are widely used in industries such as automotive, electronics, oil and gas, chemicals, food and beverage, medical equipment, mechanical engineering, and many other fields.
Advantages of U-shaped Rubber Gaskets
U-shaped rubber gaskets offer several important advantages, including:
1. Tight Sealing: U-shaped rubber gaskets are designed to create a perfect, tight gap between surfaces, preventing water, air, dust, oil, chemicals, and other liquids from leaking.
2. Good Elasticity: U-shaped rubber gaskets have high elasticity, allowing them to adapt to deformations and vibrations during operation. This ensures that the gasket maintains a tight seal and stable performance over time.
3. Chemical Resistance and Heat Resistance: U-shaped rubber gaskets are often made from synthetic rubber or silicone rubber, which offer resistance against chemical substances and can withstand high temperatures. This makes them suitable for various applications in different industries.
4. Easy Installation and Replacement: U-shaped rubber gaskets have a simple design, making them easy to install and replace. They can be cut and adjusted to specific size requirements of the application.
5. Versatile Applications: U-shaped rubber gaskets can be used in a wide range of industries and applications, from mechanical engineering, automotive, electronics, and machinery to fluid conduits, tanks, and various industrial applications.
6. Cost-Effective: U-shaped rubber gaskets are cost-effective compared to other sealing options like metal gaskets. This makes them a popular choice for many industrial applications.
However, it is important to select the appropriate type of U-shaped rubber gasket for specific application requirements and adhere to correct installation and maintenance procedures to ensure optimal performance and durability of the gasket
Points to note about U-shaped rubber gaskets
1. Choose the appropriate material: U-shaped rubber gaskets can be made from various types of rubber such as synthetic rubber, silicone rubber, nitrile rubber, fluorocarbon rubber, etc. Ensure that you select a rubber type that can withstand environmental factors such as oil, chemicals, high temperature, pressure, to meet the requirements of the application.
2. Correct size and shape: U-shaped rubber gaskets must have the appropriate size and shape for the gap or surface that needs to be sealed. Incorrect size and shape can cause leaks or fail to provide the desired sealing.
3. Accurate installation process: Installing U-shaped rubber gaskets requires an accurate and careful process. Make sure to clean the surface, remove contaminants and grease before installation. Apply sufficient compressive force to achieve a proper seal, but avoid excessive deformation or damage to the gasket.
4. Regular maintenance: To ensure optimal performance and durability of U-shaped rubber gaskets, regular inspection and maintenance are crucial. Check for signs of wear, damage, or cracking in the gasket. If any issues are detected, replace the gasket promptly to prevent leaks or system failures.
5. Adjustments when necessary: Sometimes, to achieve optimal performance, it may be necessary to adjust or customize the U-shaped rubber gasket. This may involve actions such as cutting, bending, or other machining processes to ensure the gasket fits the size and shape of the sealing surface.
• Cutting: If the U-shaped rubber gasket does not fit the specific size of the gap or surface, it may need to be cut to adjust the size. The process of cutting the rubber gasket must be done carefully and accurately to ensure proper sealing and durability.
• Bending: In some cases, to accommodate non-flat or curved surfaces, the U-shaped rubber gasket may need to be bent. This process is typically performed using appropriate tools and methods to ensure the gasket is not damaged and still maintains its sealing capability.
• Other machining: Besides cutting and bending, there may be other custom requirements for U-shaped rubber gaskets, such as hole machining, engraving, or creating special designs. This depends on the specific requirements of the application and may require professional machining to achieve the desired results.
The most important aspect is to ensure that these adjustments and modifications are carried out with accuracy and care. Improper implementation can result in leaks, loss of sealing, or gasket damage, leading to operational and usage issues
Types of U-shaped rubber gaskets mainly used
There are several types of U-shaped rubber gaskets used in industrial applications. Here are some common types of U-shaped rubber gaskets:
1. Single U-shaped gasket: This is a simple U-shaped gasket with a single curved bend. It is used in applications that require symmetrical sealing, such as door gaskets, fluid conduit gaskets, or rotating shaft gaskets.
2. Double U-shaped gasket: The double U-shaped gasket has two parallel curved bends, forming a two-layer U-shaped configuration. This provides better sealing capability and can withstand higher pressures compared to a single U-shaped gasket. It is often used in applications that require pressure resistance, such as valve gaskets, compressor gaskets, or pump gaskets.
3. U-shaped gasket with added metal ring: The U-shaped gasket has an additional metal ring inserted inside to provide increased strength and higher temperature resistance. The metal ring helps enhance the stiffness and stability of the gasket during operation. This type of gasket is suitable for applications that require heat resistance, pressure resistance, and high friction, such as engine gaskets, fuel system gaskets, or container gaskets.
4. Expandable U-shaped gasket: The U-shaped gasket has an expandable section at one end, making it easy to install and remove. This helps save time and effort in the maintenance and replacement of gaskets. It is often used in applications that require flexibility and easy access, such as tank gaskets, machinery gaskets, or gate gaskets.
Depending on the specific requirements of the application, these types of U-shaped rubber gaskets can be made from various rubber materials to meet the requirements for chemical resistance, heat resistance, hardness, and durability.
Some common rubber materials used in manufacturing U-shaped gaskets: Synthetic rubber (SBR): Synthetic rubber is flexible, pressure-resistant, and cost-effective. It is suitable for applications that do not require chemical resistance and high temperatures.
1. Nitrile rubber (NBR): Nitrile rubber has excellent resistance to oils, fats, and organic solvents. It is a common material for applications related to oil and fuel.
2. Silicone rubber (VMQ): Silicone rubber has good heat resistance, oxidation resistance, and weather resistance. It is used in applications that require high heat resistance, such as in the automotive and electronics industries.
3. Fluorocarbon rubber (FKM): Fluorocarbon rubber has excellent resistance to chemicals, oils, high temperatures, and harsh environments. It is often used in demanding industrial applications such as the oil and gas industry and chemicals industry.
4. Ethylene propylene diene rubber (EPDM): EPDM rubber has excellent weather resistance, ozone resistance, and UV resistance. It is suitable for outdoor applications and the construction industry.
5. Heat-resistant rubber (HTV): Heat-resistant rubber has high heat resistance and pressure resistance. It is commonly used in applications that require high-temperature resistance, such as in the metallurgical industry and the automotive industry.
It is important to select the appropriate rubber material based on the specific requirements of the application to ensure proper sealing and optimal performance of U-shaped rubber gaskets
Leave a Comment